Typical fire extinguishing systems found in commercial and industrial locations include sprinklers, carbon dioxide, clean agent, and dry/wet chemical agents. Another fire extinguishing technology available, but less common, is condensed aerosol. These systems take advantage of the well-established fire suppression capability of solid particulates, with potentially reduced collateral damage associated with traditional dry chemicals. However, there are some concerns in regard to collateral damage to computers and other sensitive electronic equipment.
The National Fire Protection Association (NFPA) defines condensed aerosol as an extinguishing medium consisting of finely divided solid particles and gaseous matter, generated by a combustion process of a solid aerosol forming compound. Dry chemical agents are powder based agents that normally range in diameter from 25 to 150 micrometers, while condensed aerosols are defined by NFPA as particles of less than 10 micrometers in diameter. Both produce large surface areas for reaction and are very effective extinguishants.
The fire tetrahedron identifies four elements needed for fire to occur: heat, fuel, oxidizing agent (usually oxygen), and chemical chain reaction. Fire will burn until at least one of these elements is removed. Condensed aerosol mainly interferes with the chain reaction, similar to halocarbon agents, such as Halon1301. Without the chain reaction, there’s insufficient heat necessary to maintain the fire.
Construction of Aerosol Generators
Generally, aerosol generators consist of the casing, initiation device (actuator), aerosol-forming compounds, reaction (oxidation) component, cooling component and discharge ports.
The solid aerosol generator constructed according to the principal of blast-pipe grinder which reduces the dried product to fine particles by action of jets of compressed fluid (air or nitrogen , for example) in a circular chamber called a micronizer.
Contents
The aerosol-generating chemical is a thermoplastic mixture consisting of an oxidiser, a combustible binder and additives. The oxidiser is solid potassium nitrate (KNO3), the binder is solid plasticised nitro-cellulose (CnHmNpOq) and other ingredients for stabilisation. Combustion products of the aerosol-generating chemical consists of: potassium carbonate (KHCO3, K2CO3), carbon dioxide (CO2), nitrogen (N2) and water (H2O) and represent the actual extinguishing agent, completely environmentally friendly.
Action of Generators
(a) Three potential methods of action
(b) Aerosol generation
(c) Aerosol distribution
Working Principle
The principle of the extinguishing action employed by aerosol is unique – a special solid chemical, which when electrically or thermally ignited, produces combustion byproducts – micron sized dry particles, (mainly potassium carbonates), and a gaseous mixture, (mainly carbon dioxide, nitrogen and water vapour), mixed together into a uniform fire extinguishing aerosol, before being released into the protected area. The hot aerosol propels itself through a unique solid chemical coolant, which decomposes, absorbing huge amounts of heat, thus ensuring a flameless discharge and a uniform distribution of the cool aerosol within the area. The high rate of aerosol discharge ensures a tremendous knock down effect. Micron sized aerosol particles exhibit gas-like three-dimensional qualities that allow the agent to rapidly distribute throughout enclosure and to reach even the most concealed and shielded locations. Homogenous distribution is achieved in a matter of seconds, while long holding times all help to prevent fire re-ignition.
When activated the solid aerosol element undergoes a combustion reaction, which can schematically be represented as follows:
KNO3 (s) + CnHmNpOq (s) = KHCO3 (s) + K2CO3 (s) + CO2 (g) + N2(g) + H2O (g)
Combustion products mainly consist of potassium carbonates (KHCO3 , K2CO3), carbon dioxide gas (CO2 (g)), nitrogen gas ( N2 (g) ) and water vapour (H2O(g)) and represent the actual extinguishing agent.
As the reaction temperatures are high, potassium carbonates are formed in the gas phase, but as the vapour cools, the potassium carbonates condense to a liquid and then a solid. As solid potassium carbonates are produced by condensation, the particle size is very small – approximately from 1 to 10 microns. Micron sized solid particles mix with the gaseous carbon dioxide, nitrogen and water into a uniform homogeneous gas-like phase – an aerosol.
Thus, extinguishing aerosol is a suspension of the micron sized solid particles, mainly potassium carbonates, in the gas mix of carbon dioxide, nitrogen and water vapour.
Aerosole Extinguishing Action
(i) Removal of Flame Propagation Radicals– “chain carriers” OH, H and O in the flame zone. The chemical action of potassium radicals in Pyrogen is similar to that of bromine radicals in Halons and can be schematically represented as follows:
K + OH = KOH
KOH + H = K + H2O
(ii) Recombination of flame propagation radicals– Gaseous potassium carbonates condense to a liquid and then a solid form producing a large number of micron sized particles. Being so small, the particles produce a large surface area, where recombination of “chain carriers” takes place:
O + H = OH
H + OH = H2O
Secondarily, aerosol extinguishing action is achieved by lowering fire temperature to a temperature below which the fire reaction cannot continue (thermal cooling). Several physical mechanisms can be underlined:
(a) Heat absorption via endothermic phase changes:
K2CO3 (s) —-> K2CO3 (l) —-> K2CO3 (g)
(b) Heat absorption – via endothermic decomposition reaction:
2KHCO3 (s) —-> K2CO3 (s) + CO2 (g) + H2O (g)
(iii) Dilution of the fire combustion zone by the aerosol cloud– The extremely high surface area of the micron-size aerosol particles increases the likelihood of radical recombination and heat absorbing reactions, thus ensuring rapid extinguishment with a small amount of agent. The high rate of aerosol discharge ensures a tremendous knockdown effect. Micron sized aerosol particles exhibit gas-like three-dimensional qualities that allow the agent to rapidly distribute throughout enclosure and reach the most concealed and shielded locations. Homogeneous distribution is achieved in a matter of seconds, while long holding times all help to prevent fire re-ignition.
Application
Aerosols may be used as a fixed fire suppressant system in total flooding (prime application) and local applications to fight fires of classes A, B, C, E and F. For class C fires consideration should be given to the use of vapour detection, explosion venting or explosion suppression systems where an explosion potential may exist, owing to the possible presence of gaseous, volatile or atomised fuels either before or following a fire. It may be dangerous, under certain conditions to extinguish a burning jet of flammable gases without first shutting off its supply. The design application density required to suppress normal fires involving flammable gases and liquids at atmospheric pressure shall apply if it can be shown that a potentially explosive atmosphere cannot exist in the enclosure either before or as a result of the fire.
Typical potential applications include the following normally non-occupied areas or enclosures:
- Flammable liquid storage (not requiring classified electrical equipment)
- Turbine enclosures
- Electrical cabinets
- Vehicle engine compartments
- Storage vaults
- Marine engine rooms
- CNC machines
- Aviation: aircraft dry-bays, cargo compartments, engine nacelles.
- Data centers*
- Telecommunication facilities*
* Note: although condensed aerosol manufacturers promote use in data centers and telecommunication facilities, ARC (Administrative Reforms Commission) recommends using other types of fire extinguishing systems (i.e. clean agent, etc.) based on the potential for damage to sensitive electronic equipment. Several Allianz clients have experienced corrosion damage to electronic equipment as a result of condensed aerosol system discharge.
Limitations
The protected area should not normally be occupied due to potential hazards including reduced visibility and eye irritation during and after discharge (up to one hour), potential toxic gases generated by the aerosol-generating reaction, and hot products of combustion during discharge. Personnel should not enter the area after a system discharge until the aerosol agent has settled or is properly ventilated. Condensed aerosol agents shall not be used on fires involving the following materials:
- Deep-seated fires in Class A materials (i.e. paper, wood, cloth, rubber and many plastics)
- Certain chemicals or mixtures of chemicals, such as cellulose nitrate and gunpowder, that are capable of rapid oxidation in the absence of air
- Reactive metals such as lithium, sodium, potassium, magnesium, titanium, zirconium, uranium, and plutonium
- Metal hydrides
- Chemicals capable of undergoing auto thermal decomposition, such as certain organic peroxides and hydrazine
Benefits of Aerosols Fire Suppression System
- Highest performance (3 times more effective than Halon)
- Compact and Weight Saving
- Low Toxicity
- Environmentally Friendly (0%Ozone depleting Potential)
- No Pressurised Cylinders or Pipework
- Simple to Install and commission
- Cost Effective
Arc Recommendations
Before planning to install an aerosol fire extinguishing system, please contact ARC to discuss the proposed application. In addition, the following should be thoroughly considered:
- The design, installation, maintenance, inspection and testing should be in accordance with the latest edition of NFPA 2010, Standard for Fixed Aerosol Fire-Extinguishing Systems, or equivalent standard. Submit system specifications, working plans, design calculations and manufacturer specification sheets for all equipment to ARC for review and approval prior to installation.
- Verify the protected area is not normally occupied.
- Consider the potential adverse effects of agent particulate residue on sensitive equipment and other objects. For sensitive electronic equipment (i.e. computer equipment, motor control centers (MCC), etc.), ARC recommends using other types of fire extinguishing systems (i.e. clean agent, etc.) based on the potential for corrosion damage.
- Select aerosol fire extinguishing systems listed by a nationally-recognized testing laboratory. The system shall be installed and used to protect hazards within the limitations established by the listing.
- Ensure the structural strength and integrity of the protected enclosure in the design of a total flooding system.
- Install the aerosol generators securely at a minimum safe distance from combustible materials in accordance with the manufacturer’s recommendations.
- Provide audible and visual pre-discharge alarms within the protected area to give positive warning of impending discharge.
- Develop appropriate procedures for cleaning and restoring the protected area after system discharge.
Establish a recorded maintenance program following the equipment manufacturer’s guidelines, including the following:- Monthly – verify the system is operational with no obvious deficiencies.
- Annually – have a qualified contractor inspect the system for proper operation, test the system according to the manufacturer’s procedures, and inspect the integrity of the protected enclosure.
Conclusion
Combating fires in high rise buildings has always presented serious risk to fire and rescue departments. Fires resulting from explosions are the most challenging as they can disrupt a fixed total flooding fire suppression system resulting in its failure to operate. In such cases a deployable highly efficient and rapidly delivered firefighting system could be a solution in preventing spreading of the fire and possible collapse of the building.
Incorporation of Aerosol Generators with Metal Storm Technology has created a new and novel method of firefighting, which combines superior knockdown capabilities of extinguishing aerosol with a unique method of its delivery by Metal Storm launchers. Combating high fuel loading fires in high rise buildings will continue to create challenges to fire departments in the future. A rapid deployable highly efficient firefighting system is needed. The three dimensional properties and efficiencies of aerosols agents are a sound method of combating this problem.
References
- NFPA 2010, Standard for Fixed Aerosol Fire-Extinguishing Systems
- ISO 15779, Condensed Aerosol Fire Extinguishing Systems
- ANSI/UL 2775, Standard for Fixed Condensed Aerosol Extinguishing System Units
- CEN/TR 15276-1/2, Fixed firefighting systems – Condensed aerosol extinguishing systems.
About Author:
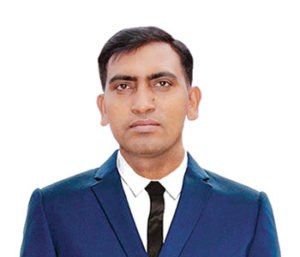
Experience : I am serving in Indian Navy Since last 15 Years and handling various fixed fire fighting (CO2 drenching system, AFFF foam System, Freon Smothering System, Water Mist System, Sprinkling System ect.) and portable fire fighting system including damage control onboard ships and establishments. I am a member of Specialist group during any emergency and exercise onboard ship. My various article as been published in Fire Engineers Magazine (Institute of Fire Engineers).